Our expertise lies in leveraging membrane technology to revolutionize process separation in the chemical and metallurgical industries. We provide efficient, selective, and energy-saving solutions tailored to separate components from complex mixtures.
In the chemical industry, we specialize in advanced membrane applications such as filtration, ultrafiltration, reverse osmosis, and nanofiltration. These technologies deliver exceptional performance in purifying, concentrating, and separating chemicals while effectively removing contaminants and unwanted byproducts. Our solutions are particularly valuable in critical areas such as wastewater treatment, solvent recovery, and the production of high-purity chemicals.
In metallurgy, we bring innovation to processes like electrodialysis and membrane distillation for metal recovery and water treatment. Our expertise lies in designing systems that separate valuable metals from ores, leach solutions, and waste streams, providing significant advantages, including reduced chemical usage, lower energy consumption, and enhanced selectivity. Our membrane separation technologies ensure the purification of process fluids, minimize environmental impact, and improve overall process efficiency
Alkaline Recovery
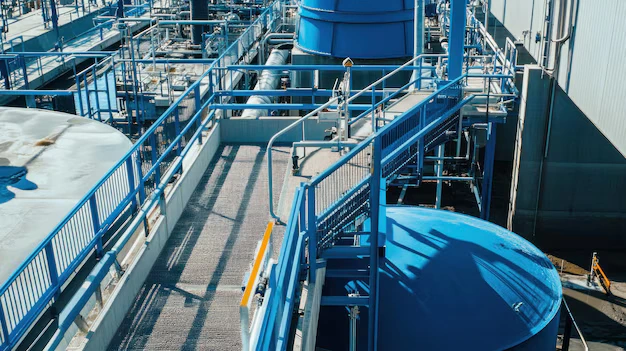
Alkaline recovery is the process of reclaiming and reusing alkaline solutions, often found in industries like wastewater treatment and chemical manufacturing. This process helps reduce operational costs and minimize environmental impact by preventing the discharge of harmful chemicals.
Membrane separation technology is instrumental in alkaline recovery, employing advanced filtration methods such as reverse osmosis, nanofiltration, and electrodialysis to selectively remove contaminants from alkaline solutions. These membrane technologies enhance the efficiency and effectiveness of recovery, allowing for higher purity and concentration of the alkaline solution, which can then be reused in industrial processes.
Process Flowchart
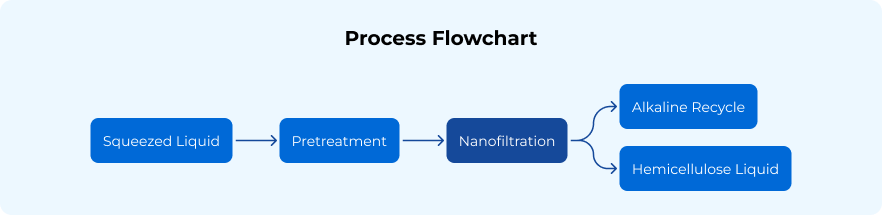
Relevant Technologies
We specialize in the application of advanced filtration methods, including reverse osmosis, nanofiltration, and electrodialysis, to optimize alkaline recovery. These membrane technologies ensure the efficient separation of contaminants, enabling the production of high-purity, concentrated alkaline solutions ready for reuse in industrial processes.
Spiral Wound Nanoflo® Membranes
Spiral Wound Nanoflo® technology are used for selective separation, allowing smaller ions and molecules to pass through while retaining larger contaminants. This process is effective for recovering alkaline solutions with moderate salinity, providing a high recovery rate with minimal energy consumption.
Electrodialysis (ED)
Electrodialysis (ED) uses an electric field to move charged particles through ion-selective membranes, separating positive and negative ions from the alkaline solution. This method is particularly useful for concentrating and recovering alkaline solutions in applications where ion removal is crucial.
Chor-Alkali Industry
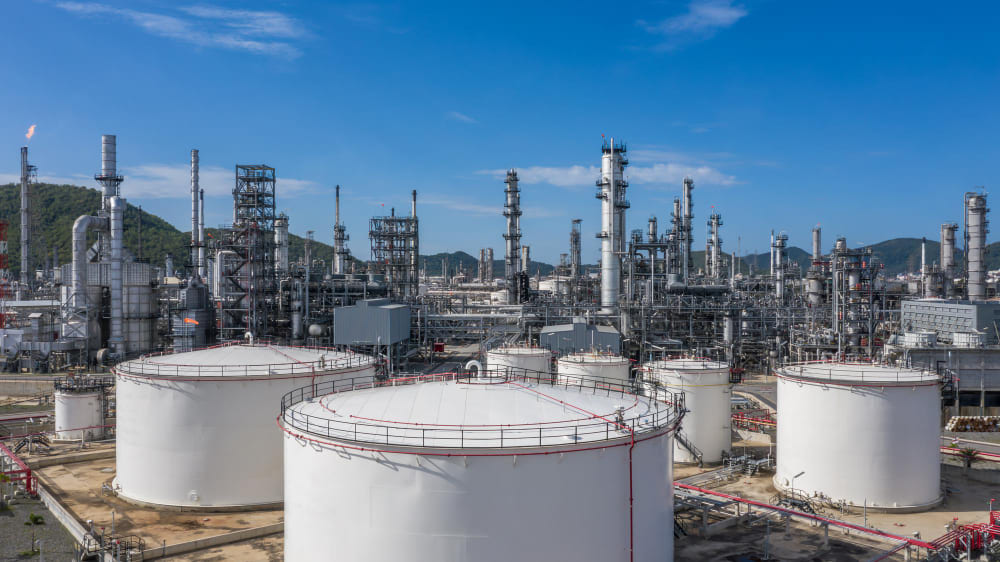
The chlor-alkali industry is responsible for producing key chemicals like chlorine, sodium hydroxide (caustic soda), and sodium carbonate. These chemicals are essential in various industries, such as water treatment, paper, textiles, and chemicals. The primary process used in the chlor-alkali industry is the electrolysis of salt (sodium chloride), which separates it into chlorine gas, hydrogen gas, and sodium hydroxide solution.
In the chlor-alkali industry, the softening process is typically used to remove hardness-causing ions, such as calcium and magnesium, from water used in electrolysis. This is important because hard water can scale and damage equipment, reducing efficiency. Softening is usually achieved through the addition of lime (calcium hydroxide) or soda ash (sodium carbonate), which reacts with the hardness ions to form insoluble precipitates that can be removed by sedimentation or filtration. This ensures that the water used in the electrolysis process remains clean, helping maintain equipment performance and prolonging the life of the plant.
Process Flowchart
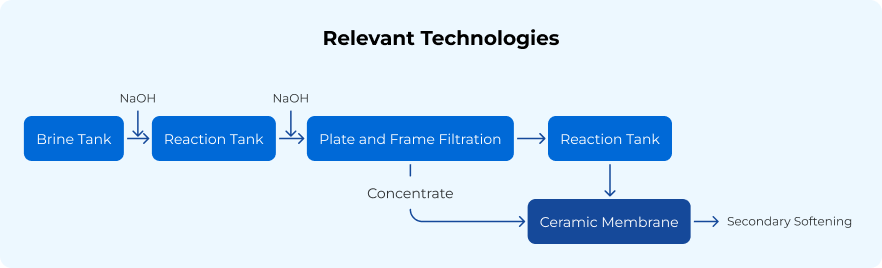
Relevant Technologies
Our expertise lies in applying membrane separation technology within this industry, including the development of a specialized softening process using membrane technology.
Ceramic Membranes
- Replace traditional sand filtration, cellulose pre-coated filters, and other equipment in the softening process.
- Shorten the overall extraction process by providing more efficient filtration and reducing the need for multiple steps.
Spiral Wound Nanoflo® Membranes
- Used to selectively remove divalent ions (such as calcium and magnesium) from the water, effectively softening the water.
- Offer a more targeted and efficient method compared to conventional chemical dosing.
Spiral Wound Reverse Osmosis (RO) Membranes
- Enables the recycling of treated water within the process, reducing overall water consumption.
- Enhances sustainability by minimizing wastewater generation and reducing the need for fresh water intake.
Dyestuff Industry
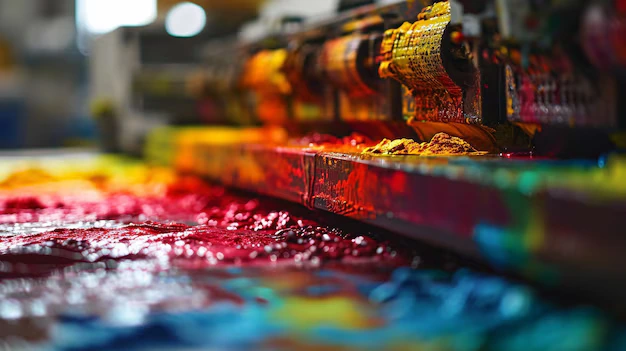
The dyestuff industry, integral to textiles, paper, and various other sectors, is characterized by high water consumption and the generation of complex wastewater containing organic dyes, salts, and chemicals. Our expertise lies in the dye post-processing stage, where we provide precise filtration to remove impurities, recover valuable dye molecules, and enhance product quality.
This technology enhances yield, optimizes production efficiency, and reduces raw material consumption, making it both cost-effective and environmentally sustainable. By significantly reducing wastewater and chemical discharges, membrane separation aligns with clean production standards, establishing itself as an indispensable solution for the modern dyeing industry.
Process Flowchart
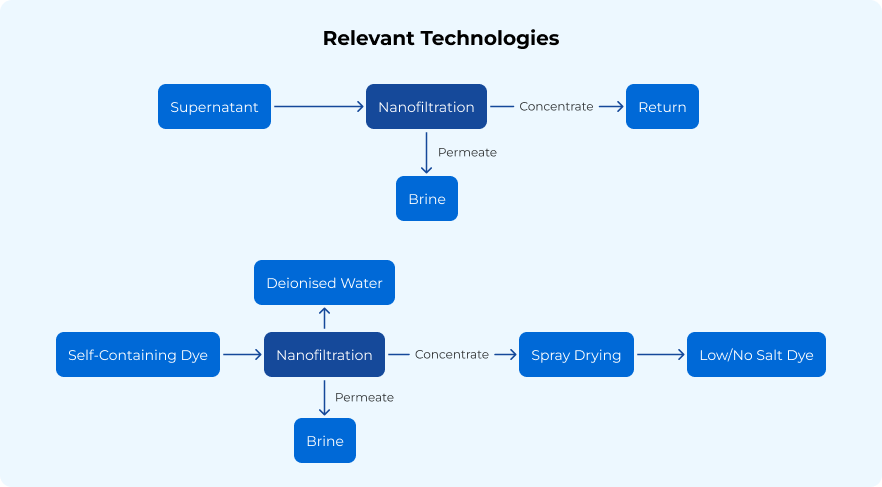