Spiral wound membranes deliver exceptional versatility, seamlessly integrating to both process separation and wastewater treatment applications.
Spiral wound membranes are a type of separation membrane that utilize a semi-permeable barrier to achieve selective filtration. These membranes are constructed with several key components: a feed spacer, a permeate spacer, and a permeate tube. The membrane is wrapped around the central permeate tube in a spiral configuration. They come in various sizes, commonly including 1812, 2540, 4040, and 8040, each suited to different applications and flow requirements.
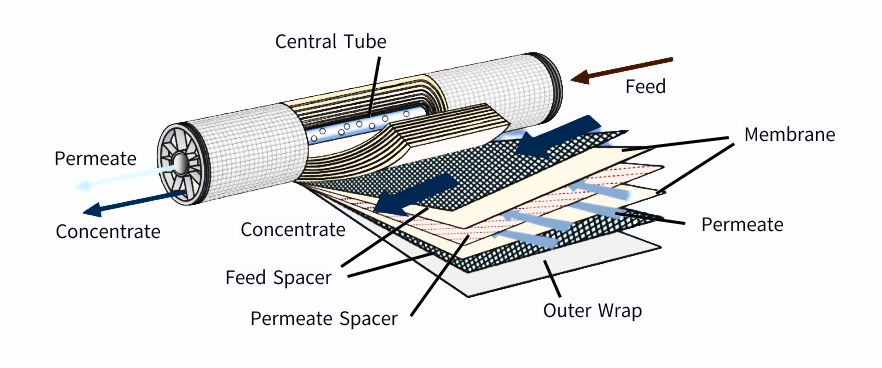
The 1812 Spiral Wound Membrane measures 12 inches in length and has a diameter of 1.8 inches. The 2540 Spiral Wound Membrane measures 40 inches in length with a diameter of 2.5 inches. This specification is primarily used for pilot testing to assess the viability of new applications. It is also used in localized settings, such as small desalination units and pure water production for laboratory use.
The 8040 Spiral Wound Membrane measures 40 inches in length with a diameter of 8 inches. The 4040 Spiral Wound Membrane measures 40 inches in a length with a diameter of 4 inches. This specification is widely used size in many industrial applications, with pressure vessels housing multiple membranes.
Applications for Spiral Wound Membrane
A broad selection of spiral wound membranes for Microfiltration (MF), Ultrafiltration (UF), Nanofiltration (NF), and Reverse Osmosis (RO) enables efficient recovery, purification, process separation, and concentration of products across industries such as food and beverage, biopharmaceuticals, chemical and metallurgy, water and waste water industry. These membranes are also suitable for water recovery applications. Various combinations of membrane materials, diameters, lengths, and spacers ensure compatibility with all cross-flow membrane filtration processes.
Key Benefits of for Spiral Wound Membrane
- A myriad of available membranes ensures excellent separation performance.
- Strong anti-fouling properties.
- Variety of feed spacers tailored to accomodate different range of viscocities and foulant present.
- Stable permeate quality, ensuring consistent and reliable output over time.
- Employs high quality raw materials, automated production lines and adhere to stringent quality management systems.